The Crucial Role of a Nozzle in an Oil Boiler: Enhancing Efficiency and Performance
- AMC
- Aug 26, 2023
- 3 min read
Updated: Sep 18, 2023
Oil boilers rely on a complex system of components to deliver the desired warmth efficiently. Among these components, the nozzle plays a crucial role in optimising the combustion process. In this blog post, we will explore the significance of a nozzle in an oil boiler and how it contributes to enhancing efficiency and performance.
Fuel Atomisation
The primary function of a nozzle in an oil boiler is to atomise the fuel. Atomisation refers to the process of breaking down the fuel into tiny droplets, facilitating better combustion. The nozzle achieves this by imparting high velocity and pressure to the fuel oil. The resulting fine mist of fuel promotes efficient mixing with air, ensuring a more complete and controlled combustion process.
Combustion Efficiency
Efficient combustion is essential for maximising the energy output of an oil boiler. The nozzle's design and characteristics significantly influence the combustion efficiency. The nozzle's spray pattern, spray angle, flow rate, and droplet size distribution all play a vital role in achieving optimal combustion. The nozzle ensures proper fuel-air mixture, preventing incomplete combustion, soot formation, and the release of harmful pollutants.
Flame Stability
A stable flame is critical for maintaining consistent heat output and reducing fuel wastage. The nozzle's ability to provide a steady and reliable fuel spray contributes to flame stability. By delivering a uniform fuel-air mixture, the nozzle helps create a stable and controlled flame pattern within the combustion chamber. This stability minimises the risk of flame disruptions, such as flame rollouts or flame impingement, which can lead to inefficient heating and potential damage to the boiler.
Energy Efficiency
Energy efficiency is a key consideration for any heating system. The proper functioning of the nozzle significantly impacts the overall energy efficiency of an oil boiler. By ensuring efficient atomisation and combustion, the nozzle helps extract more heat from the fuel, minimising waste and reducing fuel consumption. This not only translates into cost savings but also reduces the environmental impact by lowering greenhouse gas emissions.
Maintenance and Performance
Regular maintenance of the nozzle is crucial to ensure optimal boiler performance. Over time, nozzles can become clogged or worn out, leading to poor atomisation and decreased efficiency. It is important to clean or replace the nozzle as recommended by the manufacturer to maintain peak performance. Additionally, selecting the right nozzle size and type for the specific boiler application is essential for achieving the desired heat output and efficiency.
If a nozzle in an oil boiler gets clogged up, it can have several negative effects on the boiler's performance and efficiency. Here are some potential consequences:
Reduced Fuel Flow A clogged nozzle restricts the flow of fuel oil into the combustion chamber. This reduction in fuel flow can lead to a decrease in heat output, resulting in inadequate heating of the space or water. It may cause the boiler to struggle to reach the desired temperature, leading to discomfort and inefficient energy usage.
Incomplete Combustion When the nozzle is clogged, the atomisation process is hindered, and the fuel droplets may not be properly mixed with the air. This can result in incomplete combustion, leading to a yellow or sooty flame. Incomplete combustion not only reduces the boiler's efficiency but also increases the emission of pollutants such as carbon monoxide and soot, posing risks to both occupants and the environment.
Soot Buildup A clogged nozzle can cause an imbalance in the fuel-air mixture, leading to the formation of soot. Soot deposits can accumulate on heat exchanger surfaces, burner components, and flue passages, impairing heat transfer and reducing overall boiler efficiency. Additionally, soot buildup can increase the likelihood of system malfunctions, such as flame rollouts or blockages in the flue, which can be hazardous.
Increased Energy Consumption When a nozzle is clogged, the boiler has to work harder to achieve the desired heat output. The increased strain on the system can lead to higher energy consumption, resulting in elevated fuel bills. Inefficiencies caused by a clogged nozzle can also shorten the lifespan of the boiler and its components, leading to costly repairs or premature replacement.
System Breakdown In severe cases, a completely clogged nozzle may cause the boiler to shut down as a safety measure. This is typically triggered by a lack of flame detection due to insufficient fuel flow. System shutdowns not only disrupt heating but also indicate a need for immediate maintenance and nozzle replacement.
To prevent these issues, regular maintenance, cleaning and replacement of the nozzle are essential. Annual servicing and inspections can help detect and address clogs before they cause significant problems. It is also important to use high-quality fuel oil and ensure proper filtration to minimise the risk of nozzle clogging.
Contact the experts at AMC Oil Boiler Services today to book your Oil Boiler inspection and annual service.
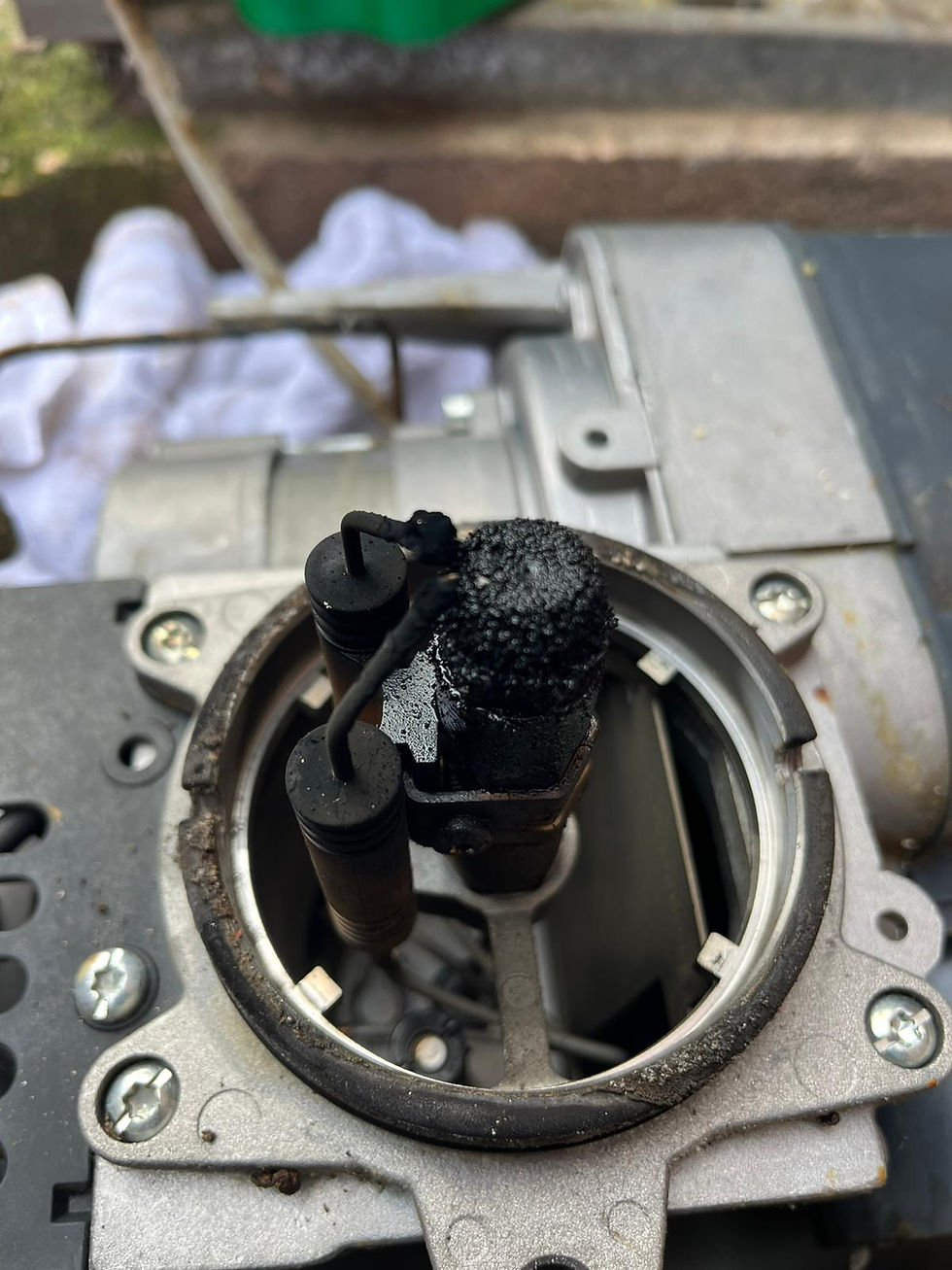
